Acrylic, also known as plexiglass, is a versatile material widely used in industries such as signage, interior design, advertising, and manufacturing. Its durability, transparency, and ease of customization make it a popular choice for a variety of applications. To achieve precise cuts and intricate engravings on acrylic, a CNC acrylic cutting and engraving machine is the ultimate tool.
CNC Acrylic Cutting Machine
A CNC acrylic cutting and engraving machine is a computer-controlled device designed to cut, engrave, and shape acrylic materials with precision. Using advanced CNC (Computer Numerical Control) technology, these machines follow pre-programmed instructions to create intricate designs, smooth edges, and detailed engravings.
Understanding the Significance of Proper CNC Router Settings for Acrylic Cutting
Achieving high-quality cuts on acrylic sheets requires meticulous attention to several CNC router settings. The primary parameters to focus on include:
- Feed-Rate: This is the speed at which the router moves across the material. An optimal feed-rate minimizes melting and chipping, which are common issues with acrylic. Generally, a feed-rate between 75-300 inches per minute (IPM) is recommended.
- RPM (Revolutions Per Minute): The spindle speed plays a crucial role in maintaining clean cuts. For acrylic, an RPM of around 18,000 is usually effective.
- Cutting Depth: The depth at which the bit penetrates the material impacts both cut quality and tool longevity. A good rule of thumb is to set the cutting depth to half the diameter of the bit being used.
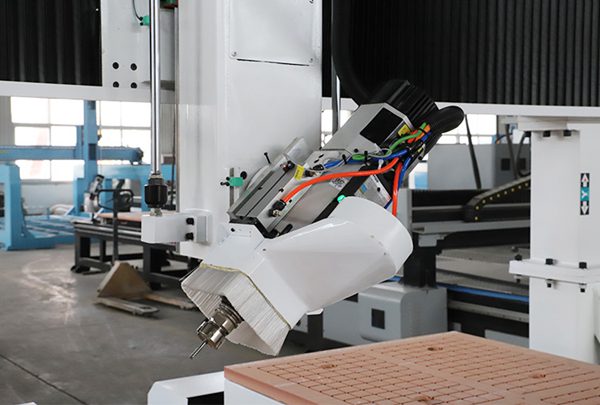
Guidelines for Setting Up Your CNC Router to Cut Acrylic
To ensure precise and clean cuts on acrylic sheets, follow these step-by-step instructions for calibrating your machine parameters:
1. Select Appropriate Bit:
- Use a 1/4-inch solid carbide O-flute bit for cutting.
- For engraving, a 60° engraving bit is ideal.
2. Adjust Feed-Rate:
- Start with a conservative feed-rate around 75 IPM and gradually increase up to 300 IPM based on test cuts.
3. Set RPM:
- Adjust your spindle speed to approximately 18,000 RPM to balance cutting efficiency and material integrity.
4. Determine Cutting Depth:
- For a 1/4-inch bit, set the cutting depth to 1/8 inch (half of the bit diameter).
5. Implement Ramping Techniques:
- Use ramping techniques during initial penetration to prevent material distortion and reduce stress on the bit.
6. Secure Material Properly:
- Ensure that acrylic sheets are firmly secured on the machine bed using clamps or a vacuum table system.
7. Perform Test Cuts:
- Conduct test cuts on scrap pieces of acrylic to fine-tune feed-rate, RPM, and cutting depth before proceeding with the actual project.
Using a high-performance CNC router can further enhance your setup’s efficiency and precision due to features like its multi-tool head and helical rack and pinion system.
Each adjustment in these settings should be approached methodically, considering the specific type and thickness of acrylic you are working with. This ensures not only optimal cut quality but also extends the life of your cutting tools.
By meticulously calibrating these parameters, you can master acrylic cutting on your CNC router, achieving professional-grade results consistently.
Applications of CNC Acrylic Cutting and Engraving Machines
1. Signage and Advertising
- Applications: Cutting letters, logos, and shapes for illuminated signs, displays, and banners.
- Benefits: Produces sharp, clean edges and professional-quality results.
2. Interior Design
- Applications: Creating decorative panels, partitions, and custom furniture.
- Benefits: Enables intricate designs and smooth finishes.
3. Acrylic Awards and Trophies
- Applications: Engraving text, logos, and designs on acrylic awards and plaques.
- Benefits: Delivers precise, elegant engravings.
4. Prototyping and Model Making
- Applications: Producing prototypes, architectural models, and product designs.
- Benefits: Allows for rapid design iterations and detailed cuts.
5. Retail Displays
- Applications: Cutting and engraving acrylic for product stands, holders, and showcases.
- Benefits: Enhances visual appeal with polished finishes.
6. Art and Crafts
- Applications: Creating custom jewelry, ornaments, and decorative items.
- Benefits: Enables intricate and creative designs.
Cutting Techniques for Achieving Clean and Precise Results on Acrylic
Best Practices for Cutting Acrylic on a CNC Router
To achieve clean cuts on acrylic sheets with a CNC router, it is essential to master several cutting techniques that minimize common issues. These techniques include:
1. Minimizing Chipping
- Use the Right Bit: Opt for a 1/4-inch solid carbide O-flute bit. This type of bit is specifically designed to efficiently evacuate chips and reduce edge chipping during the cutting process.
- Proper Feed Rate and RPM: Maintain a feed rate between 75-300 IPM and an RPM around 18,000. However, it’s important to adjust these settings based on the specific type and thickness of the acrylic being used.
2. Preventing Melting
- Cooling Systems: Implement air or mist cooling systems to manage heat buildup during the cutting process. These systems effectively prevent excessive melting.
- Sharp Tools: Ensure that cutting tools are sharp and in good condition. Dull tools generate excess heat, leading to melting.
3. Reducing Edge Burring
- Multiple Passes: Utilize multiple shallow passes instead of a single deep cut. This approach reduces stress on the material and significantly improves edge quality.
- Ramping Techniques: Apply ramping techniques when initiating cuts to prevent sudden tool engagement that can cause burring along the edges.
Ensuring Cut Quality
In addition to mastering cutting techniques, securing acrylic sheets properly on the machine bed is crucial for achieving high-quality cuts. Here are a few methods that can help:
1. Vacuum Table
A vacuum table can secure the acrylic sheet uniformly across its surface, minimizing vibrations during the cutting process. The CNC Router, which features a multi-zone phenolic vacuum table, is an excellent example of a system that accomplishes this effectively.
2. Double-Sided Tape or Clamps
For smaller pieces or intricate cuts, using double-sided tape or mechanical clamps to hold the material in place is recommended. However, it’s essential to ensure that these clamps do not obstruct the tool path.
3. Edge Supports
When working with thin sheets, utilizing edge supports is crucial to prevent flexing during the cut. This helps maintain consistent pressure and significantly reduces the risk of cracks or breaks.
For additional insights into optimizing your production line and selecting suitable products for your projects, you might find these resources helpful:
- Tips for Your Cabinet Making Production Line: Cabinet woodworking demands time, patience, and persistence. This resource provides valuable tips to enhance your cabinet making production line.
- IGOLDENCNC Product Range: IGOLDEN is a leading manufacturer of CNC routers, laser engraving machines, plasma cutters, and other equipment. Their product range offers various options for different applications.
By mastering these cutting techniques and implementing appropriate securing methods, you can achieve clean, precise results while maintaining the integrity of your acrylic sheets. This combination of proper bit selection, machine settings, and securing techniques enhances both efficiency and quality in your CNC routing projects.
Types of CNC Acrylic Cutting and Engraving Machines
Router CNC Machines
- Features: Uses a rotary spindle with cutting bits to carve and shape acrylic.
- Best For: Thick acrylic sheets and large-scale projects.
- Advantages: Handles heavy-duty tasks and offers versatility for other materials.
Laser CNC Machines
- Features: Uses a high-powered laser beam to cut and engrave acrylic.
- Best For: Intricate designs, polished edges, and detailed engravings.
- Advantages: Non-contact cutting ensures no material deformation.
Benefits of Using a CNC Acrylic Cutting and Engraving Machine
1. Precision and Accuracy
- Produces clean, polished edges and detailed engravings without the need for post-processing.
2. Versatility
- Handles a wide range of acrylic types and thicknesses, making it suitable for diverse applications.
3. Efficiency
- Automates cutting and engraving processes, reducing production time and labor costs.
4. Customization
- Allows for unlimited design possibilities, perfect for personalized and custom projects.
5. Cost-Effectiveness
- Minimizes material waste and eliminates the need for manual labor, saving money in the long run.
6. Scalability
- Suitable for both small-scale projects and high-volume production.
FAQs (Frequently Asked Questions)
1. What materials can a CNC acrylic cutting and engraving machine handle?
In addition to acrylic, these machines can cut and engrave materials like wood, plastic,mdf, and thin metals, depending on the model.
2. How much does a CNC acrylic cutting and engraving machine cost?
Prices range from $500 for entry-level models to over $20,000 for industrial-grade machines.
3. Do I need prior experience to use a CNC acrylic cutting machine?
No, many models are beginner-friendly and come with tutorials and pre-set programs. However, learning basic CAD software is helpful.
4. How do I maintain a CNC acrylic cutting machine?
Clean the machine regularly, replace worn parts, and follow the manufacturer’s maintenance guidelines.
5. Can a CNC acrylic cutting machine handle mass production?
Yes, industrial-grade machines are designed for high-volume production and can operate continuously.
IGOLDEN BLOG
Thank you for visiting the iGOLDENCNC website. iGOLDENCNC is the professional supplier of CNC machinery application solution, within the business of producing and selling CNC machinery and accessories.